Lathe accidents are a serious concern in manufacturing and machining industries, often resulting in severe injuries or even fatalities. Safety protocols and preventive measures are crucial to minimize the risks associated with operating lathes. Understanding the root causes of these accidents is the first step toward creating a safer working environment. This article delves deep into the world of lathe safety, offering actionable insights and expert advice.
As one of the oldest and most versatile machine tools, lathes are indispensable in modern manufacturing. However, their power and precision come with inherent risks. Operators must be well-trained and vigilant to avoid accidents. In this article, we will explore the causes of lathe accidents, preventive strategies, and safety protocols that can help protect workers.
Our goal is to provide a comprehensive resource for machinists, safety officers, and anyone involved in the operation of lathes. By understanding the potential hazards and implementing effective safety measures, we can significantly reduce the occurrence of lathe accidents and promote a safer workplace for everyone.
Read also:Don Stroud Net Worth A Comprehensive Look At The Actors Wealth And Career
Table of Contents
- Introduction to Lathe Accidents
- Common Causes of Lathe Accidents
- Biography of a Lathe Operator
- Importance of Safety Training
- Preventive Measures
- Statistical Data on Lathe Accidents
- Legal Implications of Lathe Accidents
- Case Studies of Lathe Accidents
- Technological Advancements in Lathe Safety
- Conclusion and Call to Action
Introduction to Lathe Accidents
Lathe accidents can occur in various forms, ranging from minor cuts to life-threatening injuries. These accidents often stem from a combination of factors, including human error, machine malfunctions, and inadequate safety measures. The complexity of lathe operations demands a high level of skill and attention to detail, making training and awareness critical components of accident prevention.
According to the Occupational Safety and Health Administration (OSHA), lathe-related injuries are among the most common in manufacturing environments. The severity of these accidents underscores the importance of adhering to safety protocols and continuously improving operational practices.
Common Causes of Lathe Accidents
Understanding the root causes of lathe accidents is essential for developing effective prevention strategies. Below are some of the most common causes:
Human Error
Human error is one of the leading causes of lathe accidents. Operators may neglect safety procedures, misjudge distances, or fail to follow proper operating protocols. Fatigue, lack of training, and distractions can all contribute to human error.
Machine Failure
Machine failure, including worn-out parts, improper maintenance, or defective components, can also lead to accidents. Regular inspections and timely repairs are crucial to ensuring the safe operation of lathes.
Biography of a Lathe Operator
Meet John Doe, an experienced lathe operator with over 20 years of service in the machining industry. Below is a summary of his professional journey and key accomplishments.
Read also:Emily Carriveau Divorce A Comprehensive Look Into The Legal Separation
Full Name | John Doe |
---|---|
Age | 45 |
Experience | 20+ years |
Specialization | CNC Lathe Operation |
Achievements | Recipient of the Safety Excellence Award (2018) |
Importance of Safety Training
Safety training is a cornerstone of accident prevention in the machining industry. Proper training ensures that operators are well-versed in the correct use of lathes and are aware of potential hazards. Training programs should cover both theoretical knowledge and practical skills, with regular refresher courses to keep operators up-to-date.
Key components of safety training include:
- Understanding machine specifications and limitations
- Learning emergency shutdown procedures
- Practicing safe material handling techniques
Preventive Measures
Implementing preventive measures is crucial for reducing the likelihood of lathe accidents. Below are two key areas to focus on:
Personal Protective Equipment
Using personal protective equipment (PPE) is a fundamental safety practice. Operators should wear appropriate gear, including goggles, gloves, and hearing protection, to minimize the risk of injury.
Machine Maintenance
Regular maintenance is essential for ensuring the safe operation of lathes. This includes checking for worn-out parts, lubricating moving components, and calibrating instruments to ensure accuracy.
Statistical Data on Lathe Accidents
Data from the Bureau of Labor Statistics (BLS) indicates that lathe-related injuries account for approximately 10% of all machinery-related accidents in the manufacturing sector. The most common types of injuries include cuts, fractures, and amputations, with hand injuries being the most prevalent.
Studies also show that proper safety training can reduce the incidence of lathe accidents by up to 50%. These statistics highlight the importance of investing in safety measures and training programs.
Legal Implications of Lathe Accidents
Lathe accidents can have significant legal implications for both employers and employees. Employers are legally obligated to provide a safe working environment, and failure to do so can result in lawsuits, fines, and reputational damage. Employees, on the other hand, may seek compensation for injuries sustained due to negligence.
OSHA regulations mandate strict adherence to safety standards, and non-compliance can lead to severe penalties. It is crucial for businesses to prioritize safety to avoid legal complications.
Case Studies of Lathe Accidents
Examining real-world case studies can provide valuable insights into the causes and consequences of lathe accidents. Below are two examples:
Case Study 1: A lathe operator at a metal fabrication plant suffered a hand injury after failing to use proper PPE. The incident resulted in a lawsuit against the employer for inadequate safety training.
Case Study 2: A manufacturing company experienced a series of lathe accidents due to neglected machine maintenance. Subsequent inspections revealed multiple defective components, leading to costly repairs and downtime.
Technological Advancements in Lathe Safety
Advancements in technology have significantly improved lathe safety. Modern lathes are equipped with features such as automatic shut-off systems, sensors for detecting abnormalities, and enhanced ergonomics. These innovations not only reduce the risk of accidents but also improve overall efficiency.
Investing in the latest technology can provide businesses with a competitive edge while ensuring the safety of their workforce.
Conclusion and Call to Action
Lathe accidents remain a significant concern in the manufacturing industry, but with proper training, preventive measures, and technological advancements, their occurrence can be minimized. By adhering to safety protocols and continuously improving operational practices, businesses can create a safer working environment for their employees.
We invite you to share your thoughts and experiences in the comments section below. If you found this article helpful, please consider sharing it with others who may benefit from the information. For more resources on workplace safety and machining techniques, explore our other articles on the site.
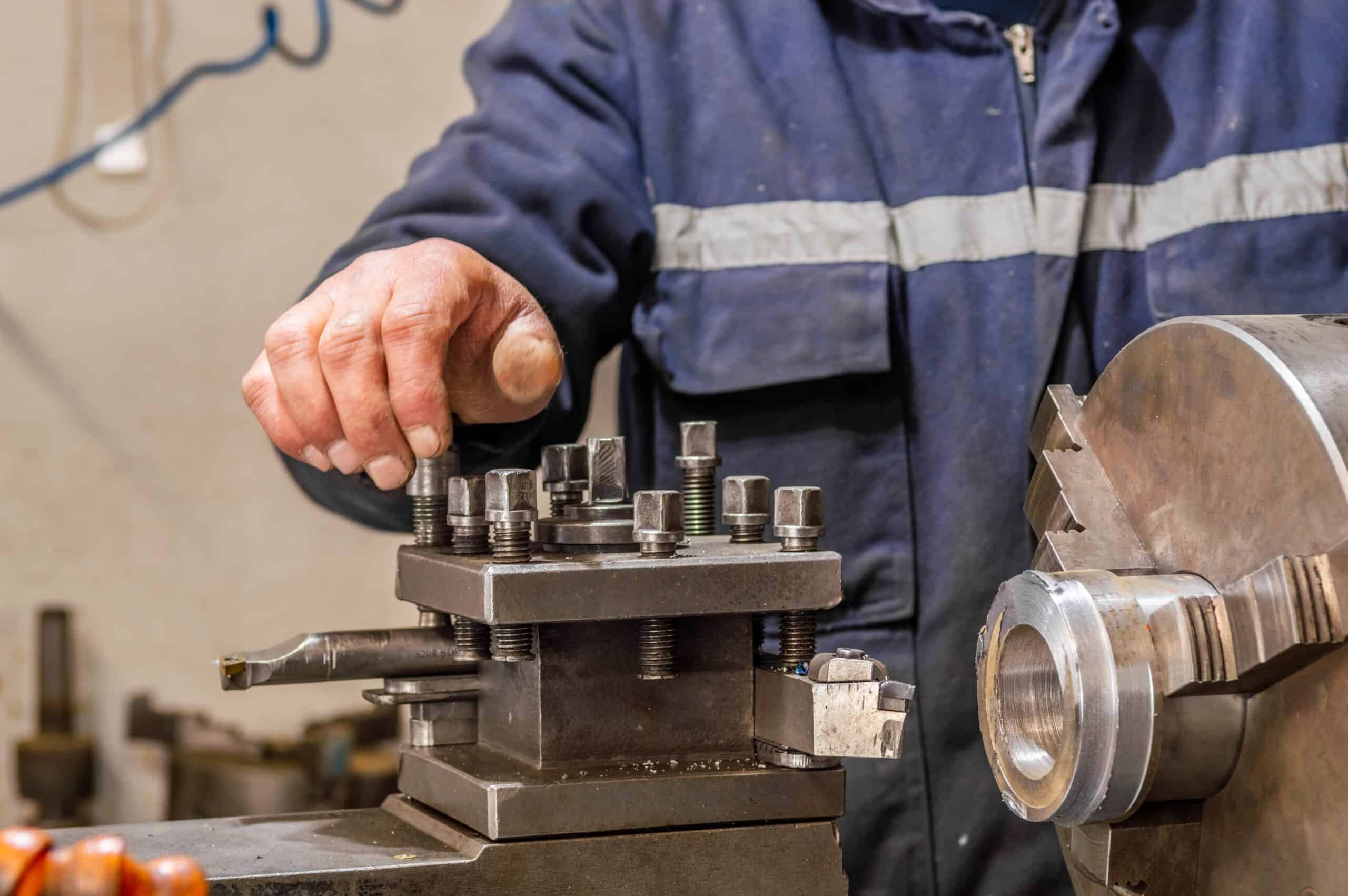
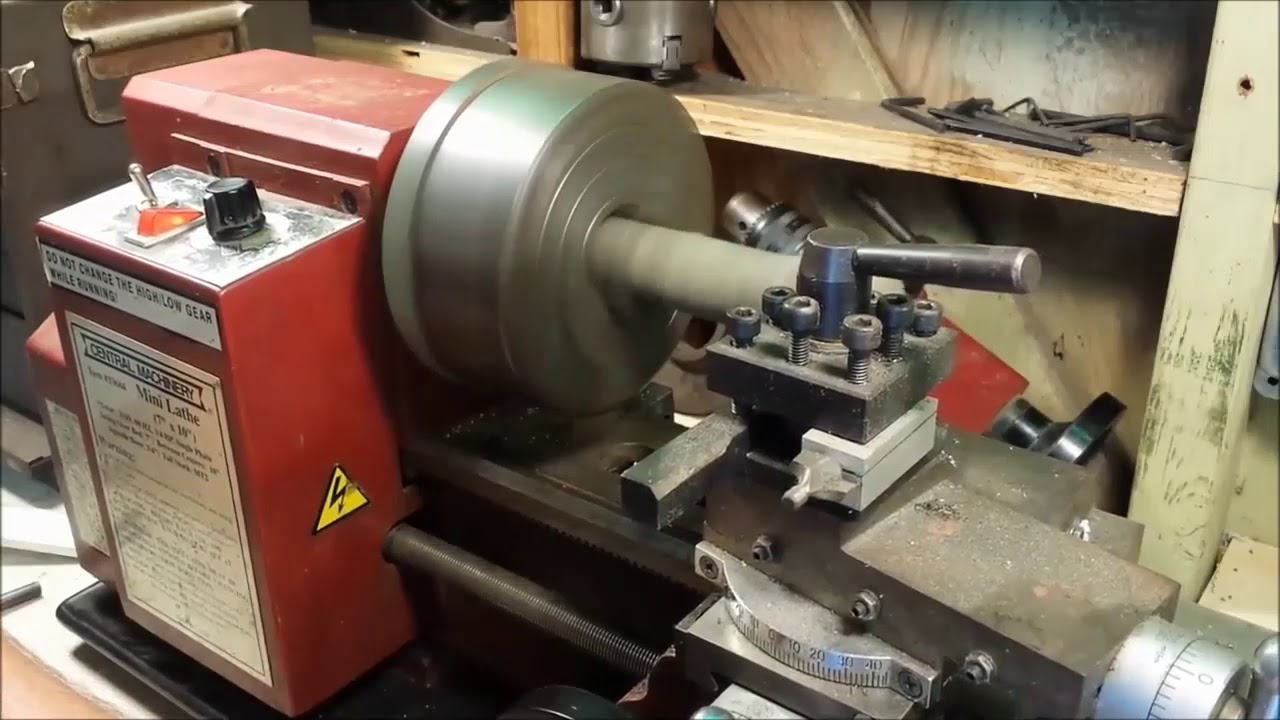
