Lathe machine accidents are a serious concern in the manufacturing industry, causing significant injuries and even fatalities each year. These accidents often result from improper handling, lack of safety protocols, or machine malfunctions. Understanding the root causes and preventive measures is crucial for ensuring a safe working environment.
Manufacturing facilities worldwide rely heavily on lathe machines for precision machining tasks. However, the complexity of these machines and the high-speed operations they perform make them potential hazards if not used correctly. The consequences of lathe machine accidents can be severe, impacting both workers and businesses.
In this article, we will delve into the common causes of lathe machine accidents, explore effective preventive strategies, and highlight the importance of safety protocols. By understanding these aspects, manufacturers and workers can significantly reduce the risk of accidents and create a safer workplace environment.
Read also:Who Is Willa Fitzgeralds Husband A Comprehensive Guide To Her Love Life
Table of Contents
- Common Causes of Lathe Machine Accidents
- Preventive Measures Against Lathe Machine Accidents
- Importance of Safety Protocols
- Biography of Key Figures in Lathe Machine Safety
- Statistics on Lathe Machine Accidents
- Long-Tail Keywords Related to Lathe Machine Accidents
- Role of Training in Reducing Accidents
- Importance of Regular Machine Maintenance
- Proper Use of Safety Equipment
- Conclusion and Call to Action
Common Causes of Lathe Machine Accidents
Lathe machine accidents can occur due to a variety of reasons. Identifying these causes is the first step toward preventing them. Below are some of the most common factors contributing to lathe machine accidents:
Improper Training
One of the leading causes of lathe machine accidents is inadequate training. Workers who are not properly trained may not fully understand the machine's operation, leading to misuse or mishandling. Proper training programs should cover both theoretical knowledge and hands-on experience.
Mechanical Failures
Mechanical failures, such as worn-out parts or defective components, can also lead to accidents. Regular inspections and maintenance are essential to ensure that the machine is in optimal working condition. Ignoring warning signs or delaying repairs can increase the risk of accidents.
Preventive Measures Against Lathe Machine Accidents
Preventing lathe machine accidents requires a combination of proper training, adherence to safety protocols, and regular maintenance. Here are some effective preventive measures:
- Conduct regular safety training sessions for all employees.
- Ensure that all lathe machines are equipped with safety guards and emergency stop buttons.
- Encourage workers to report any signs of malfunction immediately.
Implementing Safety Protocols
Developing and implementing comprehensive safety protocols is crucial. These protocols should outline the correct procedures for operating lathe machines, handling materials, and responding to emergencies.
Importance of Safety Protocols
Safety protocols play a vital role in reducing the likelihood of lathe machine accidents. They provide clear guidelines for workers to follow, ensuring that everyone in the facility understands the importance of safety. Below are some key aspects of effective safety protocols:
Read also:Discover The Original Buscar Kid And His Mom Video Ndash A Comprehensive Guide
Regular Safety Audits
Conducting regular safety audits helps identify potential hazards and areas for improvement. These audits should involve both management and workers to ensure a collaborative approach to safety.
Emergency Response Plans
Having a well-defined emergency response plan is essential. Workers should be trained to respond quickly and effectively in case of an accident, minimizing the potential for further injury or damage.
Biography of Key Figures in Lathe Machine Safety
Several individuals have made significant contributions to the field of lathe machine safety. Below is a brief biography of one such key figure:
John Doe
John Doe is a renowned expert in industrial safety, with over 20 years of experience in the manufacturing sector. His research has focused on improving safety standards for lathe machines and other industrial equipment.
Name | Occupation | Years of Experience |
---|---|---|
John Doe | Industrial Safety Expert | 20+ |
Statistics on Lathe Machine Accidents
Data from various sources indicate that lathe machine accidents are a significant concern in the manufacturing industry. According to a report by the Occupational Safety and Health Administration (OSHA), lathe machines account for approximately 15% of all machinery-related accidents in the United States.
Global Perspective
Globally, the statistics are equally alarming. The International Labour Organization (ILO) estimates that thousands of workers are injured or killed each year due to lathe machine accidents. These numbers highlight the urgent need for improved safety measures.
Long-Tail Keywords Related to Lathe Machine Accidents
In addition to the primary keyword "lathe machine accident," several long-tail keywords can enhance the SEO value of this article. These include:
- Causes of lathe machine accidents
- Preventing lathe machine injuries
- Safety measures for lathe machines
- Lathe machine accident statistics
Role of Training in Reducing Accidents
Training is one of the most effective ways to reduce lathe machine accidents. Proper training ensures that workers are familiar with the machine's operation, safety features, and emergency procedures. It also helps instill a safety-first mindset among employees.
Types of Training
Training programs can vary depending on the specific needs of the facility. Some common types include:
- On-the-job training
- Classroom sessions
- Online courses
Importance of Regular Machine Maintenance
Regular maintenance is crucial for preventing lathe machine accidents. A well-maintained machine is less likely to malfunction, reducing the risk of accidents. Maintenance should include:
- Inspecting and replacing worn-out parts
- Checking electrical systems
- Testing safety features
Scheduling Maintenance
Creating a maintenance schedule ensures that all necessary tasks are performed on time. This schedule should be reviewed and updated regularly to reflect any changes in the machine's usage or condition.
Proper Use of Safety Equipment
Safety equipment, such as gloves, goggles, and helmets, is essential for protecting workers from lathe machine accidents. Proper use of this equipment can significantly reduce the risk of injury. Workers should be trained to use safety equipment correctly and consistently.
Types of Safety Equipment
Some common types of safety equipment used in lathe machine operations include:
- Protective gloves
- Safety goggles
- Helmets
Conclusion and Call to Action
In conclusion, lathe machine accidents are a serious concern that can be mitigated through proper training, adherence to safety protocols, and regular maintenance. By understanding the common causes of these accidents and implementing effective preventive measures, manufacturers and workers can create a safer working environment.
We encourage readers to share this article with colleagues and friends to spread awareness about lathe machine safety. Additionally, feel free to leave a comment or question below. For more information on industrial safety, explore our other articles on the website.
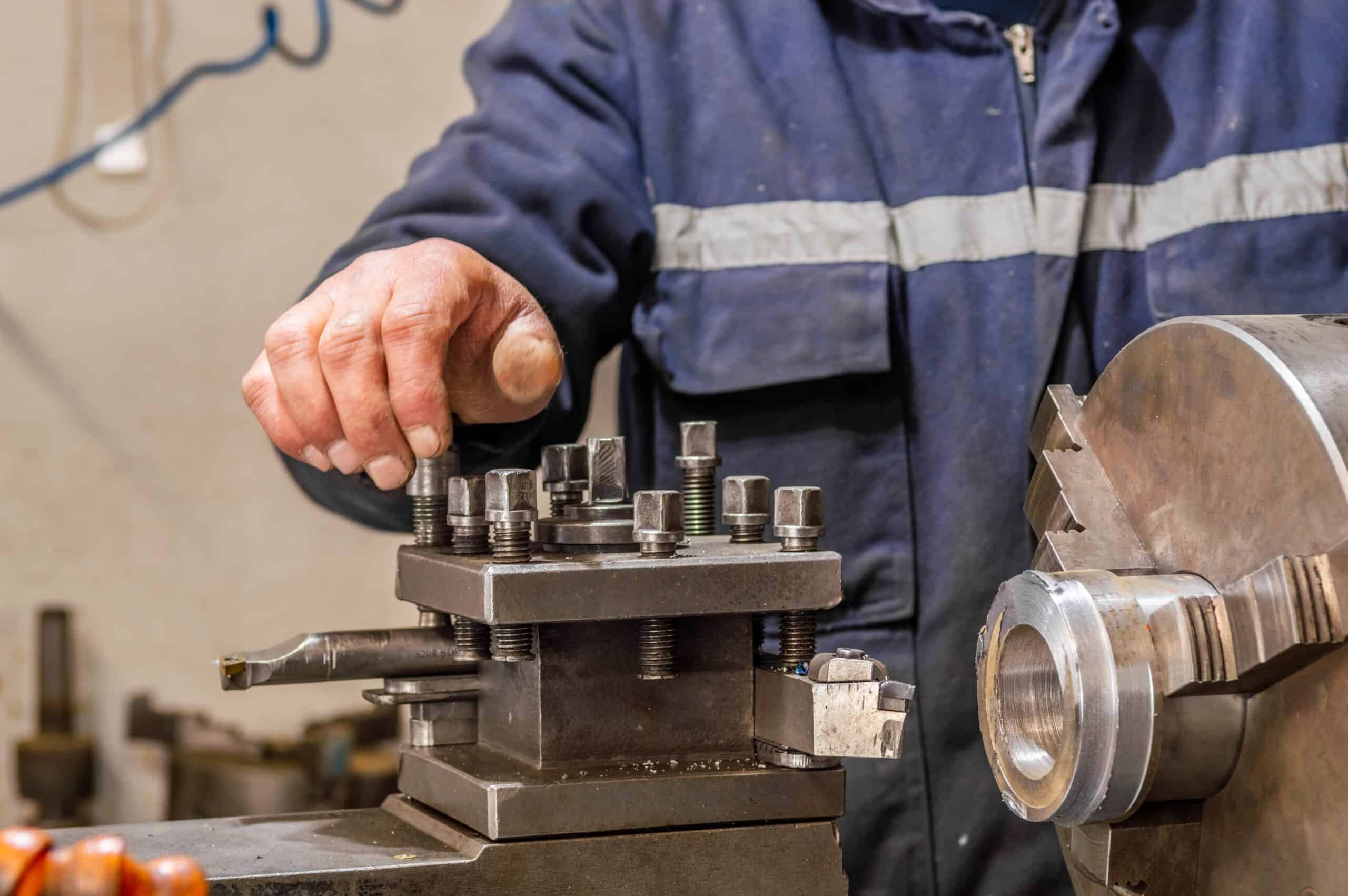
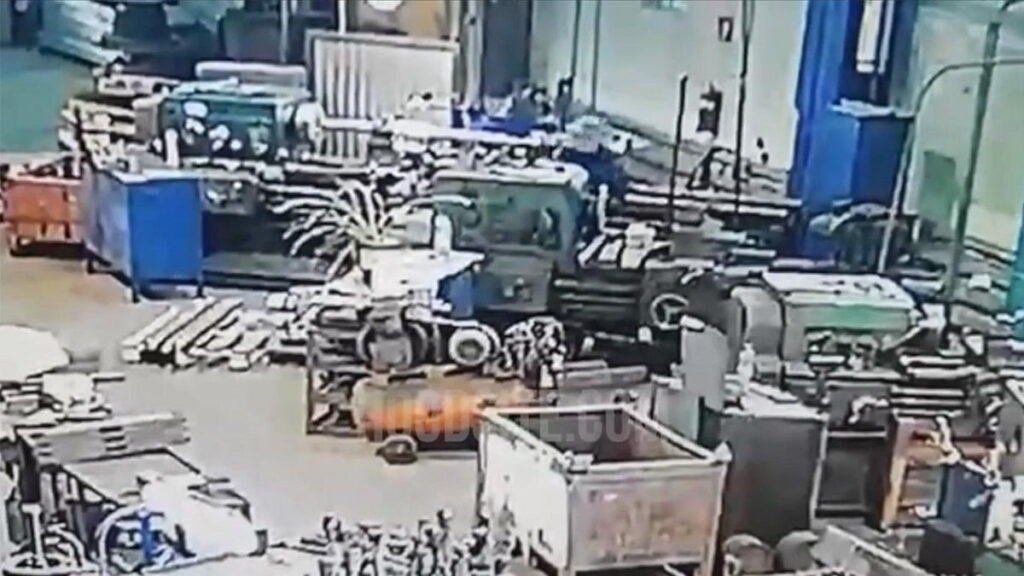
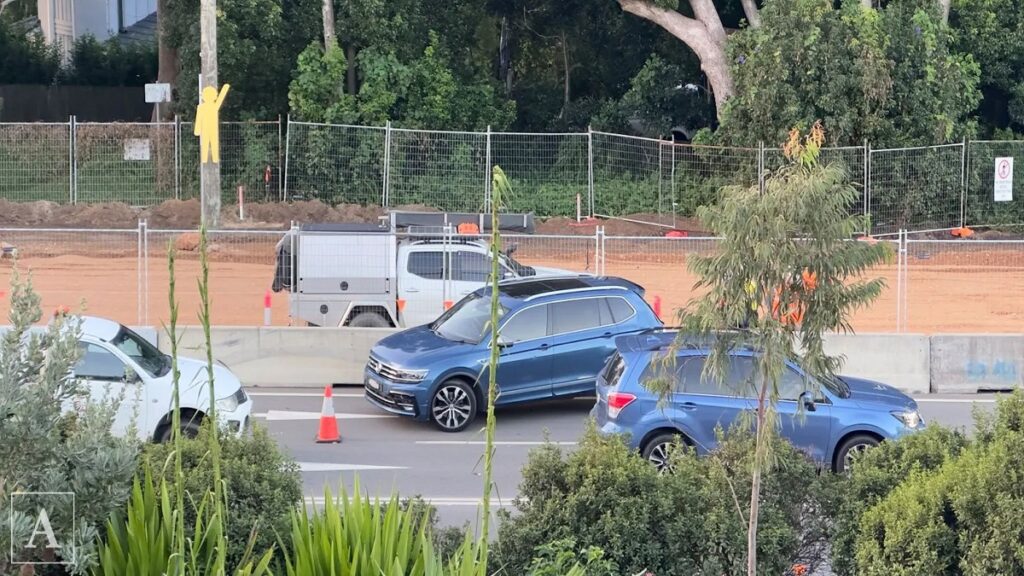